15 years of professional and powerful ODM and OEM factories are our strong support. Over 4,000 square meters of standardized production workshop, 17 sets of bonding and composite production lines,the annual production capacity has reached 1.5 billion RFID tags. 24-hour non-stop production, orders are available all year round.
Equipment Display
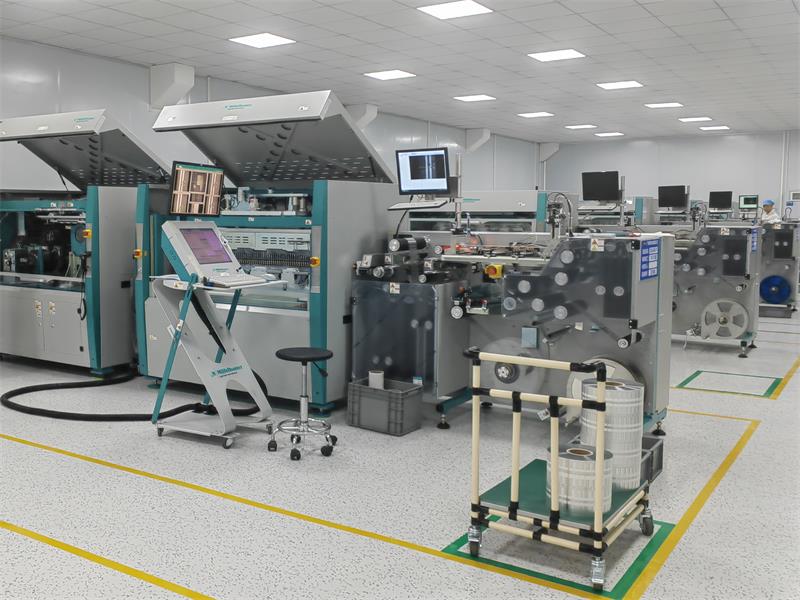
RFID Bonding Equipment
We have 5 sets of the most advanced RFID flip chip bonding equipment (DDA40K) from Germany Muehlbauer company.
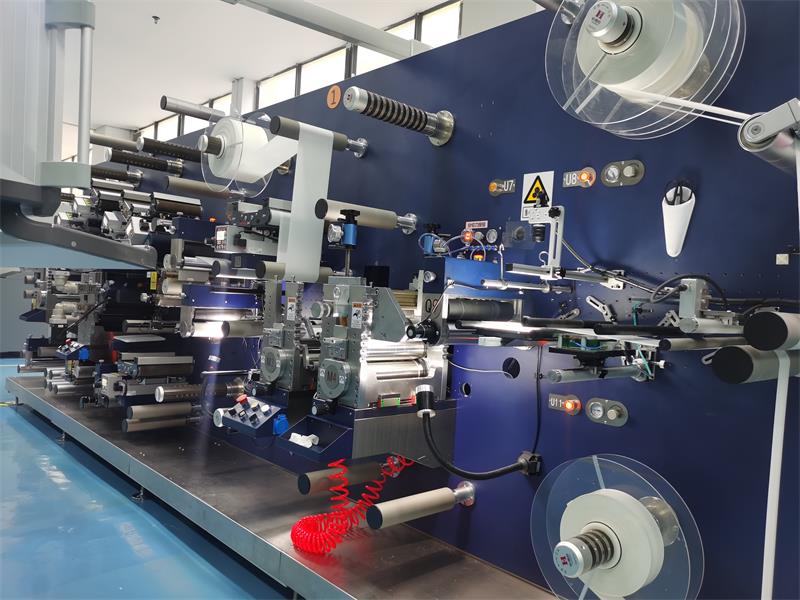
RFID High Speed Composite Equipment
We have 11 sets of composite equipment, which are equipped with the most advanced RFID on-line monitoring equipment, Voyantic.
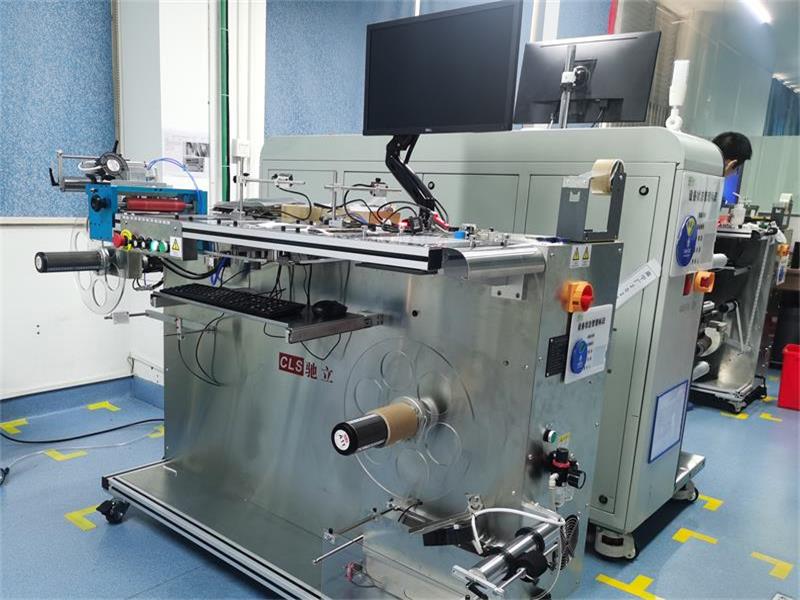
RFID Label High Speed Quality Inspection Equipment
The label inspection equipment can simultaneously encode on the label, and complete the calibration of the code content written on the label surface.

RFID Label High Speed Quality Inspection Equipment
The inspector can pick out the bad-looking labels quickly.
Production & QC teams
Production Team
Alex Wang is a production operator with 6 years of working experience, Now he has successfully become a captain of composite machine. "As for the selection of production captain, we must constantly improve our ability in the production process to win the support of team members and finally become the leader of the group." Wang said, "We will regularly learn the theory of products and machinery, in order to provide our customers with faster delivery and better quality through technical control on the assembly line." XGSun's production team has strong organizational ability and perfect production management system. We can realize the standardized processes of RFID chip bonding, label compound & die-cutting, RFID label code printing & data initialization, woven label production and other more customized process.
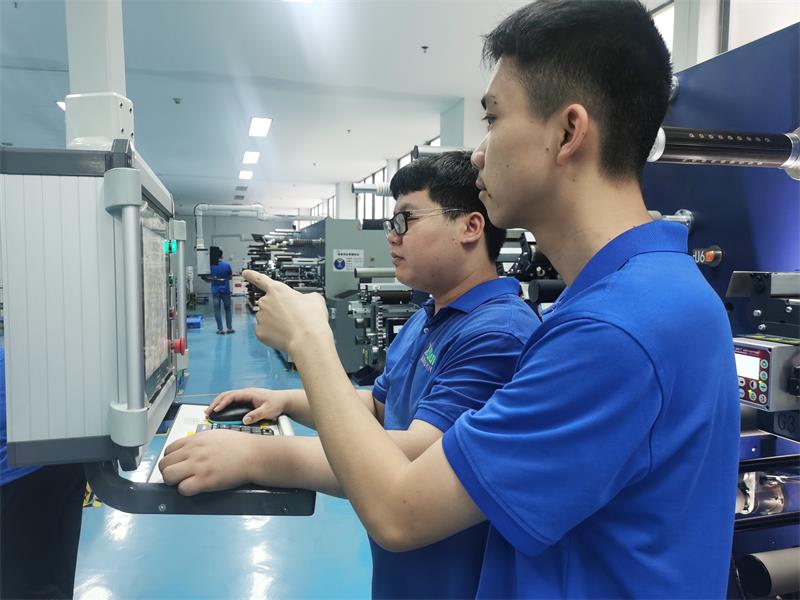
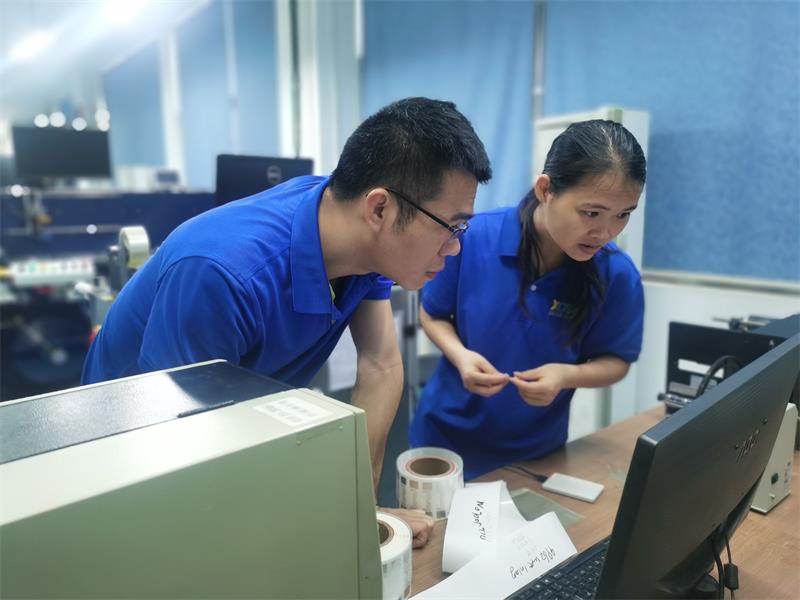
QC Team
"We are the best doctor in the RFID industry. Every qualified factory product must be carefully certified by our team. We focus not only on the readability of the product, but also on the quality control in the production process and the impact of the production environment on the quality of the finished product, "said Kai. As the quality supervisor, he has successfully ensured the quality control of no less than 500 shipments from April 2013 to now. "Our team strictly controls the temperature and humidity of the workshop environment and carries out vacuum treatment on the packaging of shipping labels to prevent the yellowing and wrinkling of RFID labels caused by the change of temperature and humidity. Every RFID label should be proofread twice after the completion of printing and writing the data on label to prevent the error. Our team's efforts are aimed at bringing the best RFID to our customers." Kai and his QC team have been controlling the quality of products with the most stringent international standards.